For the production of FK Visors, we’ve opted to automate only some of the production processes, leaving important and delicate stages like beveling and other key steps in the skilled hands of our artisans, right through to quality control, which is meticulously carried out on each individual visor. This attention to detail is the true added value that distinguishes an FK product.
The FK VISORS R&D department constantly tests and researches new materials to offer its customers increasingly higher performance.
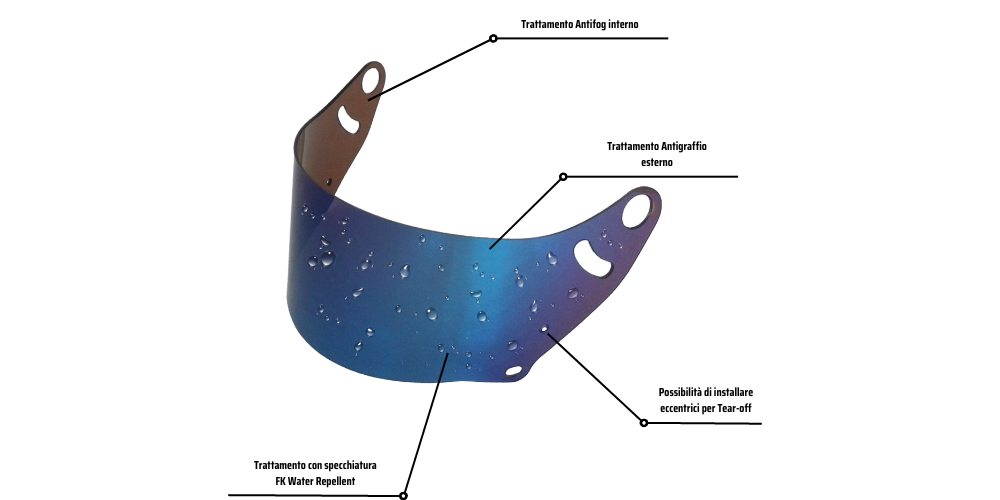
I materiali da noi utilizzati sono al 90% MADE IN JAPAN e i trattamenti antifog-antigraffio (coatings) sono inclusi nelle lastre.
- Simple polycarbonate slabs without any coating
- Polycarbonate slabs with anti-scratch coating on one side or on two sides
- Polycarbonate slabs with external antiscratch and internal antifog coatings
- Triacetate slabs with photocromatic and antifog
- Triacetate slabs with photocromatic, polarizing and antifog coatings
- Thickness: 1 mm, 1.5mm, 2mm, 3mm
- Basic colors: transparent, light fumè 50%, bronze fumè 70%, dark fumè 80%, orange
- 0.6 mm thick sheets with antifog coating, in transparent, yellow and orange
- 0.6 mm thick sheets with antifog coating and photocromatic , in transparent
- 1.2 mm thick sheets with antifog and photocromatic coating, in transparent and pink
- 1.2 mm thick sheets with antifog coating and photocromatic and polarizing , in transparent
- Transparent polycarbonate tear-offs with thickness of 125 or 175 micron
- Transparent crystal polyester tear-offs with thickness of 130 micron
- New PLA or eco-friendly material
- Lamination kit of 5 tear-offs
Made by acetate or triacetate with 0.6 mm of thickness and 3M adhesive template (perfect adhesion and resistance)
CRAFTSMAN EXCELLENCE
Here you can find the work processes made by hand from FK Visors craftsman
DEBURRING
The production department can choose to made this stage by hand or through anthropomorphic robot. The visor lines are bevelled and this make the edges plainer and perfectly compatible with the helmet.
COUNTERSUNK
The visor hole are reamed and countersunk to obtain the right rotation and facilitate the assembly.
QUALITY CONTROL
The final quality control assure that the visor is free of scratches, imperfections and is suitable for packaging